Internal robotic weld build-up of Pressure Vessel flange
Using robot welding can reduce shut-down time drastically
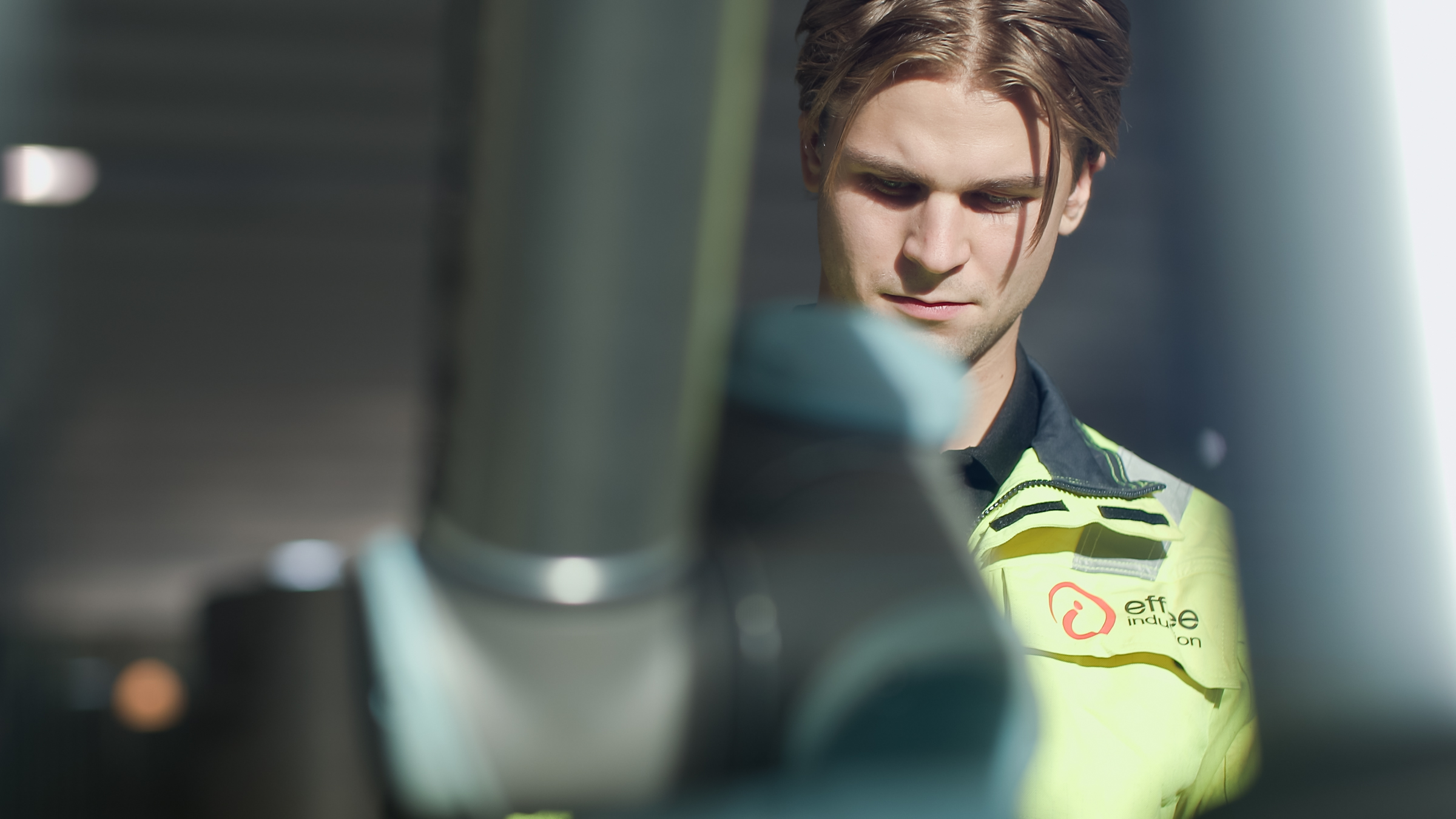
No items found.
1.2
Ton of filler metal
22.5
Km weld
4.5
Days spent welding
70
Percent time reduction
Due to internal corrosion of the a deaerator on an on-shore plant, Effee was contracted to butt-weld in a special flange on the horizontal part of pressure vessels, this to build up material thickness to a minimum as original thickness. This was carried out using a welding robot that hung from a specially made bracing that was mounted on the flange. Only one welding procedure was used, which was specifically for this purpose. The welding procedure also included post-weld heat treatment (PWHT), carried out with by subcontractor. The flange surface was finally machined due to corrosion of the flange surface, as well as large dimensional deviations from its original design.
No items found.
Get in touch
Let's talk
We'll call you to explore what robotic welding can do for your operations.